High Quality CBD
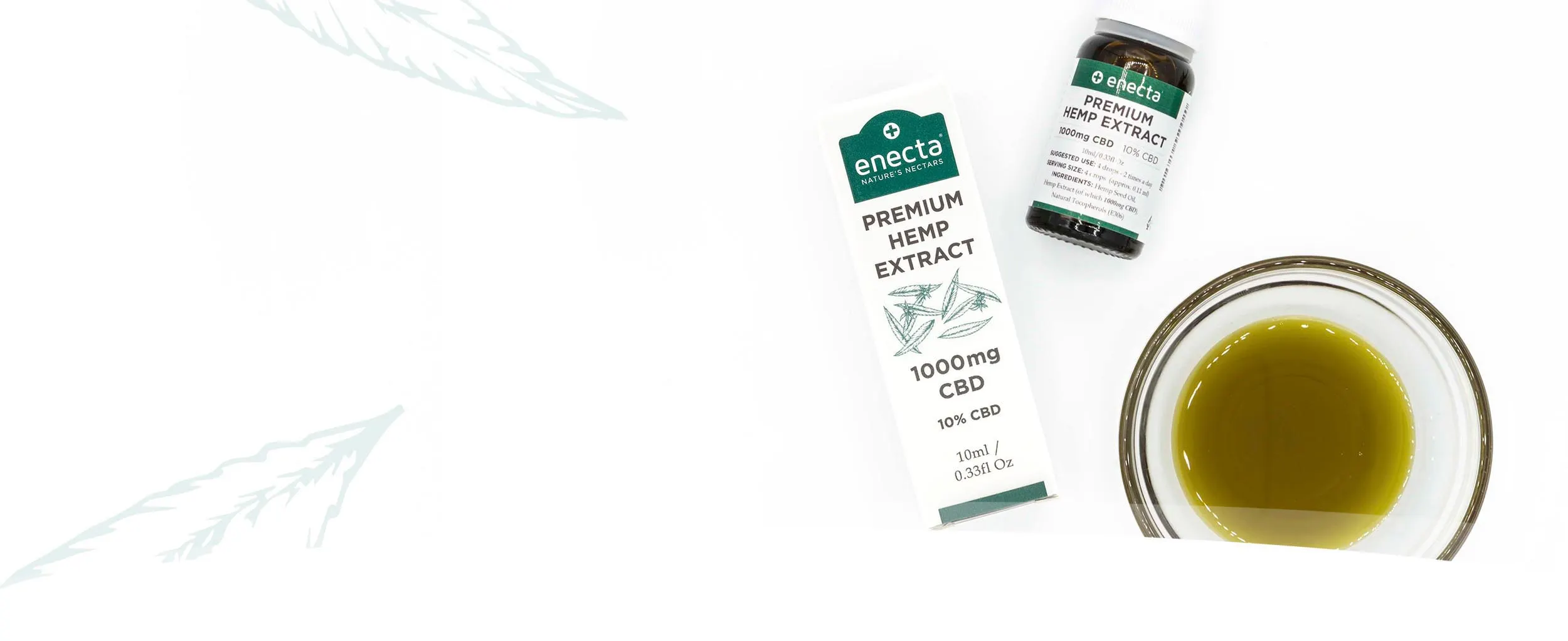
How do we produce our CBD oil?
Creating high quality CBD oil and products, like those from Enecta, requires skills, procedures and equipment that are fit for purpose. Nothing is left to chance. Since we know how essential it is to buy and consume with total peace of mind, it only seems right to explain the journey that takes a seed of Cannabis Sativa L. to becoming CBD extract, ready for consumption.
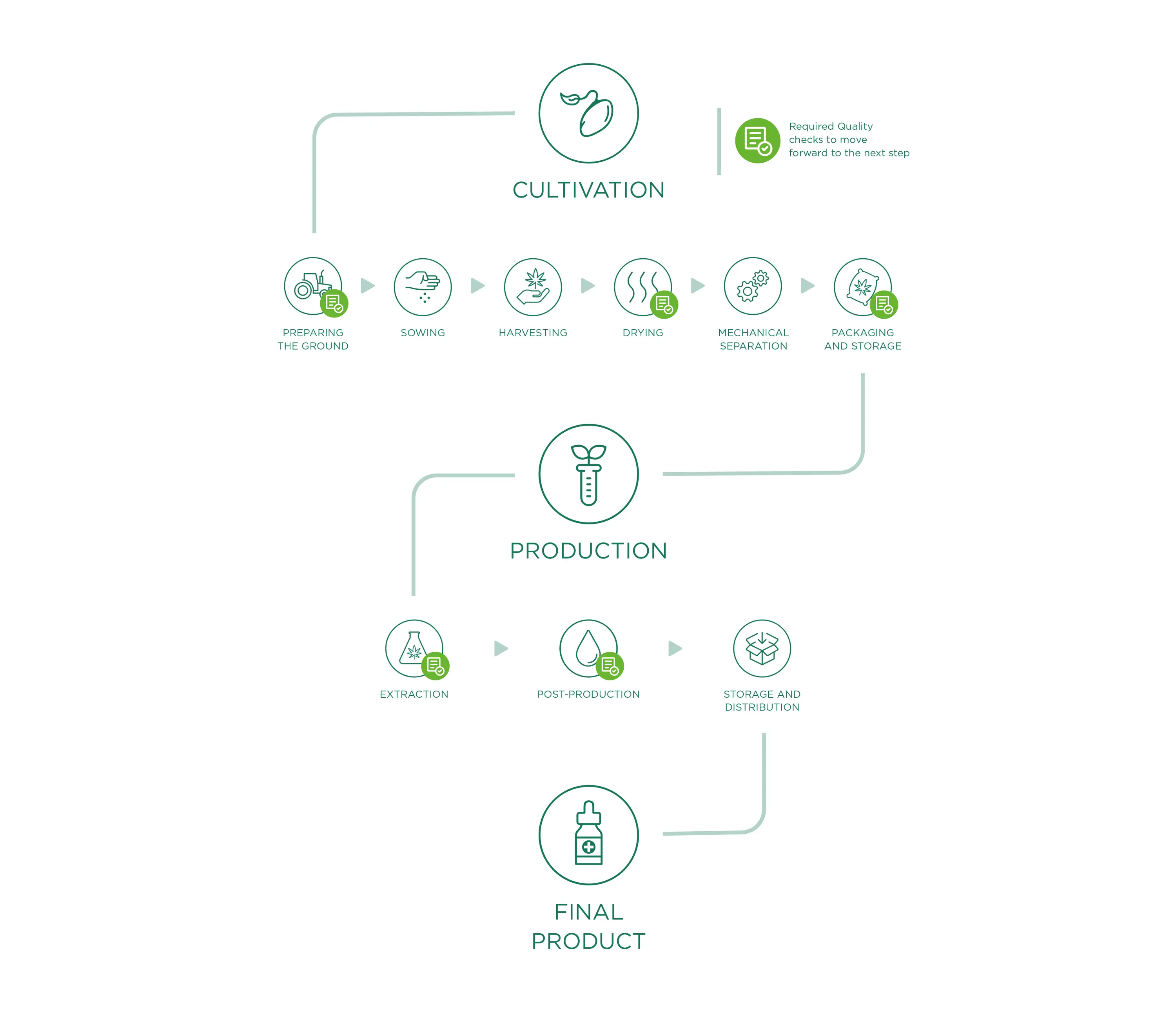
Creating a high quality product requires adhesion to some basic principles, principles that are sometimes enclosed within guidelines created by independent bodies.
The fundamental principles that guide our production are:
- Growing in selected fields without using pesticides
- Applying Guidelines on Good Agricultural and Collection Practices (GACP)
- Monitoring contaminants according to the specifications of the European Pharmacopoeia
- Good Manufacturing Practices
GACP and GMP guidelines act as a basis for the establishment of an appropriate Quality Assurance system, providing useful principles to guarantee fixed standards, ensuring:


- That general and specific hygiene requirements are observed (which includes contamination/cross-contamination, personal hygiene and a sanitary production of plant material).
- Control methods
- Documented procedures (SOP) that cover the entire production process in detail
- Safety of the process
- Suitability of the final product.
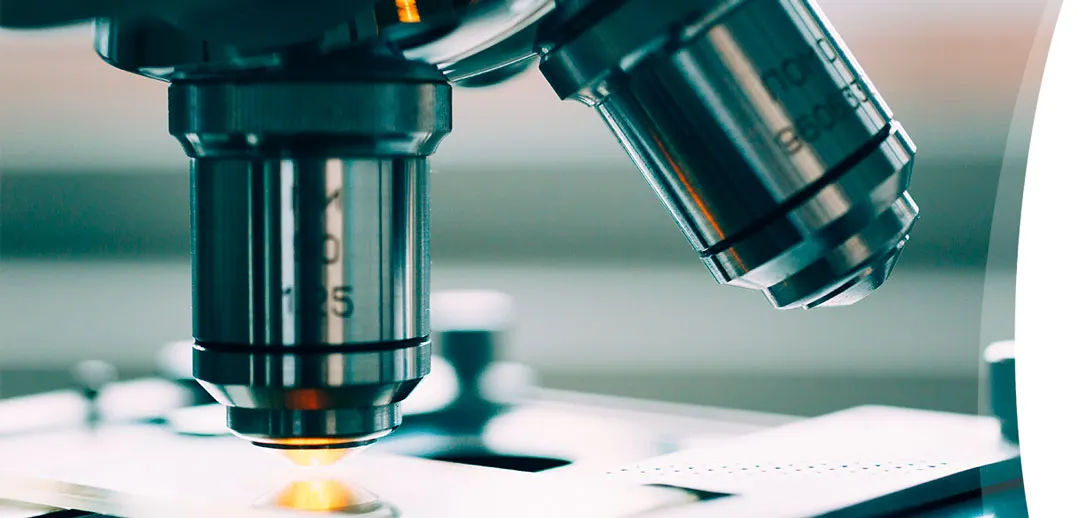
Meeting GACP and GMP guidelines: enectas Cannabis plants guaranteeing high quality of CBD Products like CBD Oil. This policy helps us ensure, through standardised procedures and by identifying critical production phases (based on the HACCP, Hazard Analysis and Critical Control Points procedures), that the quality and safety of our products is appropriate and consistent, within a complete and up to date internal tracking system (every production lot is trackable and identifiable to the producer and, therefore, to the field and exact place where the plants were grown and harvested).
Our products (in addition to following the GACP guidelines) are certified: Made in Italy, Pesticide Free, Heavy Metal Free (we guarantee the absence of heavy metals through analysis and sampling during the production phases) and Monitored Warehouse (our buildings are constantly cleaned, ventilated and controlled, with specific work areas that are well delimited and suited to protecting products from any kind of potential contamination).
Cultivation
The starting material for all Enecta products is the Cannabis Sativa L. This outstanding plant has many different varieties, each variety (also called "strain") has peculiar characteristics. Enecta has since 2013 invested in a program of seed genetic research to develop hemp plants specifically suited to the production of cannabinoids. To ensure a perfect CBD oil, we make sure that the right Cannabis seed is sowed, this is perhaps the most important decision we have to make each year.
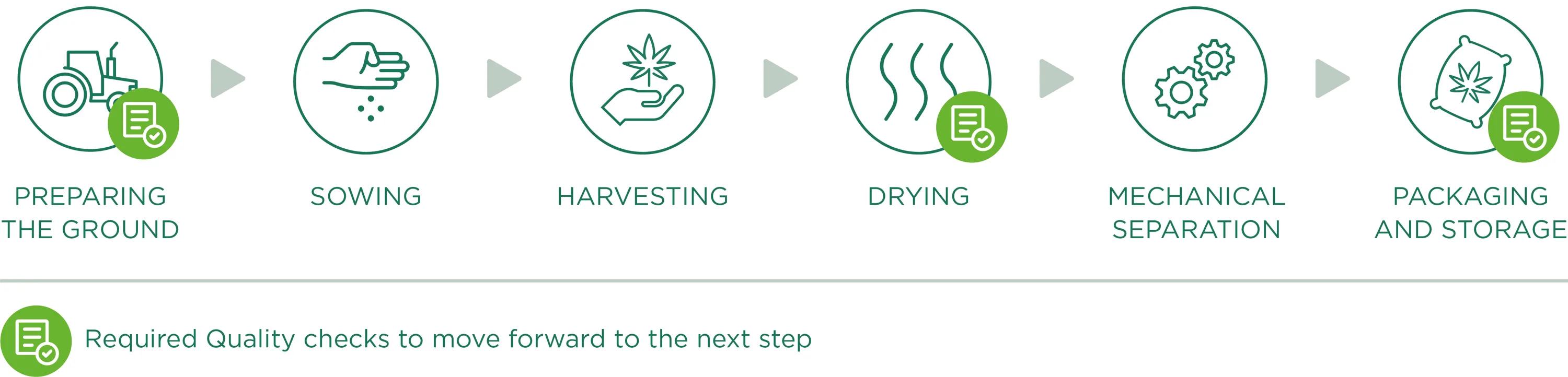
Preparing the ground
Preparing the ground for sowing, is the starting point and one of the fundamental factors of the production phase: a good field (in terms of composition, nutrients and contaminants) will indeed be able to produce a good product. Therefore, we work to create a “hospitable” soil that will become the natural habitat for roots, creating optimal conditions for growing with careful and precise monitoring to prevent weeds from growing or the presence of contaminants.
Sowing
We only plant industrial varieties registered in the European Catalog of Varieties of Agricultural Plant Species, in accordance with the13th June 2002 European Council 2002/53/CE Directive, art. 17, with a level of THC lower than 0.2% (accurately identified and certified seeds). All information relating to the land lots dedicated to hemp cultivation are registered and documented, from the their location to plant growth conditions, for a continuous monitoring of crop growth.
We emphasise that we do not use pesticides or other chemical substances as they are not essential to the development and protection of crops. In addition, thanks to continuous analyses carried out in the fields, we check the quality and potential needs and/or deficiencies during the vegetative phase. In addition, these analyses represent the basis for the ampling of Cannabinoids, which allows us to evaluate the percentage of active ingredients present during the plants growth and consequently, to decide what is the right moment to harvest.
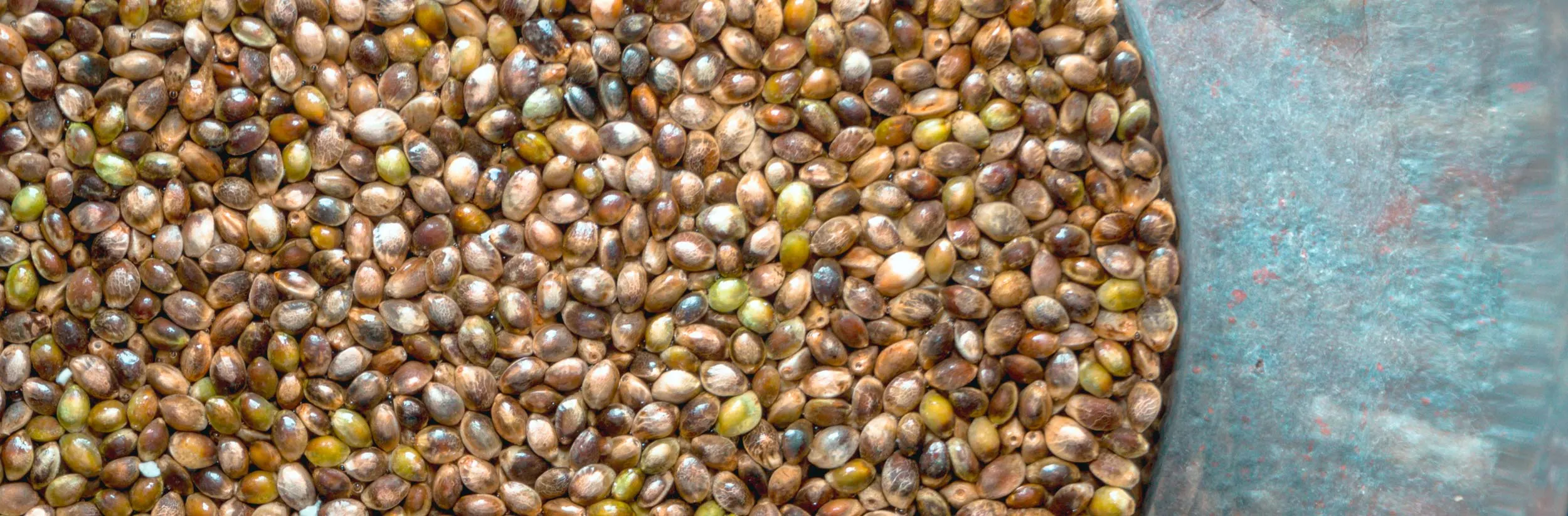
Harvesting
Harvesting occurs through specific agricultural equipment that cuts the Cannabis Sativa L. plants and directly moves them towards a trailer to the side, as the plants are slowly cut. During this phase (as for all the work phases), we place a lot of importance on cleaning all machinery/equipment that come into contact with vegetable material, so as to avoid the risk of contamination before, during and after harvesting.
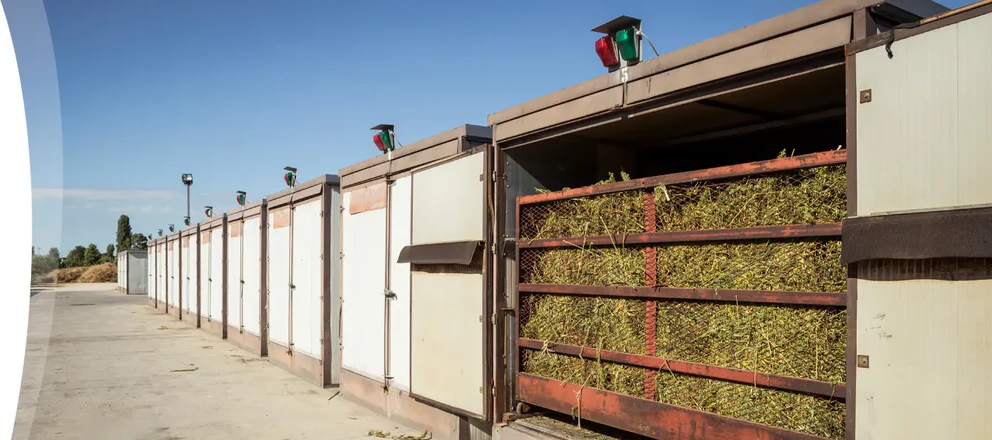
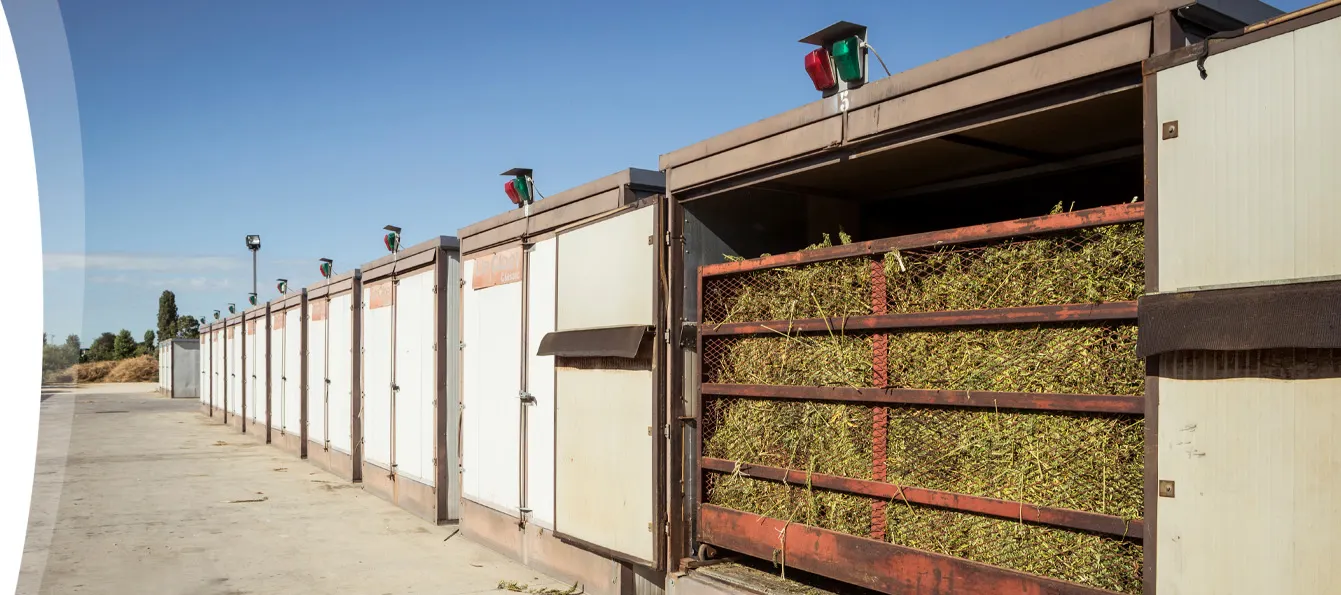
Drying
In order to obtain a product that meets the required quality standards, the drying process plays a fundamental role so that any type of degradation, alteration or contamination of Cannabis Sativa L. plants is avoided. After being harvested, the plant material is transported (in dry and clean conditions) to drying sites specifically dedicated to hemp processing. The drying phase, being a crucial point of hemp processing and consequently, for the quality of the final product, is carefully monitored, especially through continuous control of fundamental parameters like temperature and drying time, air circulation and the relative humidity of the dryer.
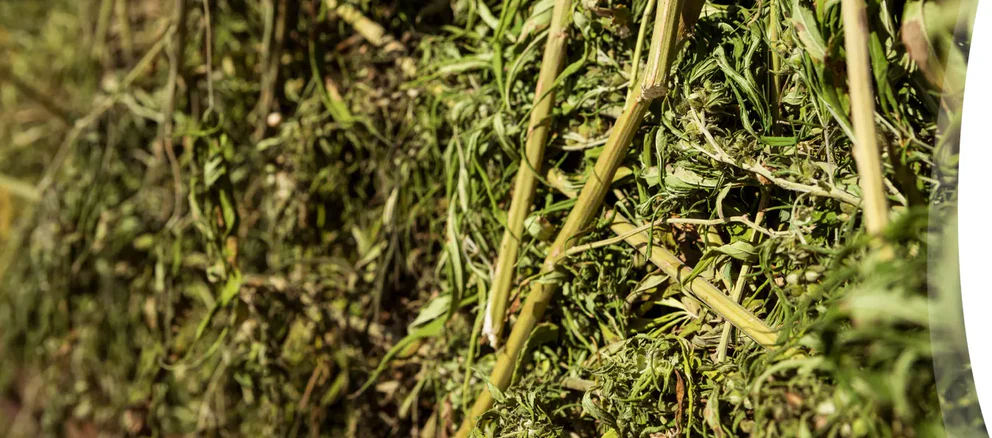
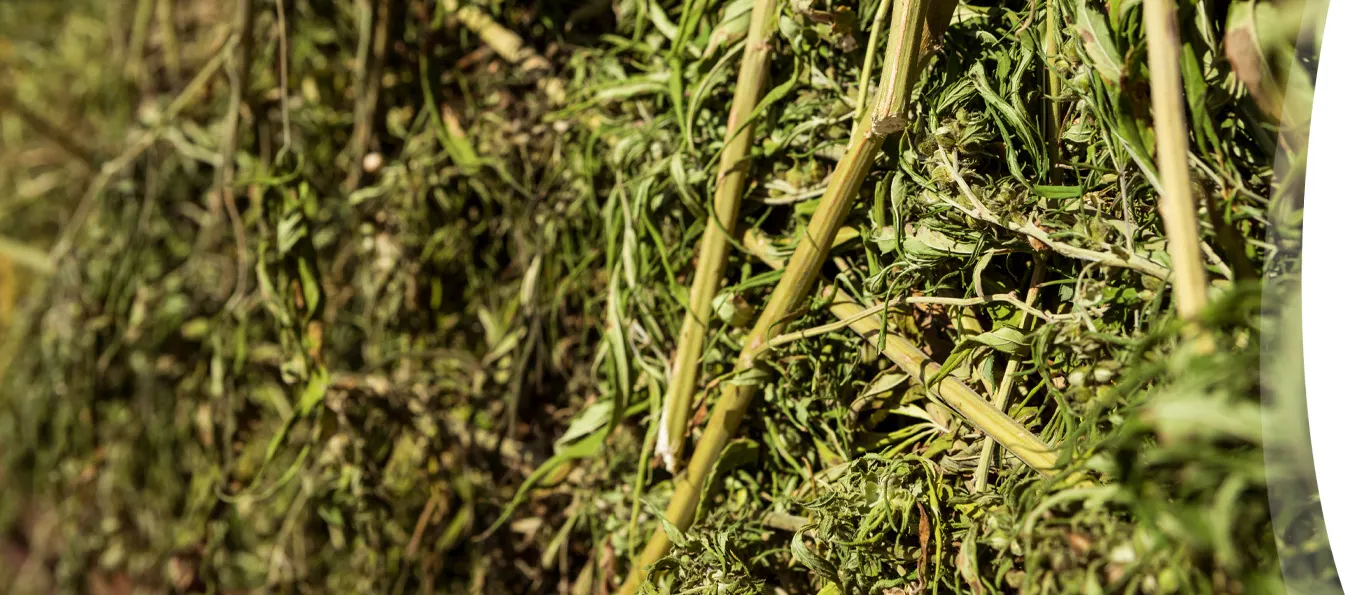
Monitoring these three factors represents an operational guarantee to obtain a uniformly dried finished product, prevent potential mould to form and contaminate the whole plant material and allow for correct and adequate preservation over time.
Mechanical separation
Once dried, the material undergoes mechanical separation. This processing phase allows the plant material to be perfectly separated through a machine that works automatically by rubbing brushes and passing through vibrating sifts and fixed sieves. Once the mechanical process is complete, the waste material will be completely separated from the perfectly ground material useful for our purposes (active ingredients extraction) which will be packaged and stored.
Packaging and Storage
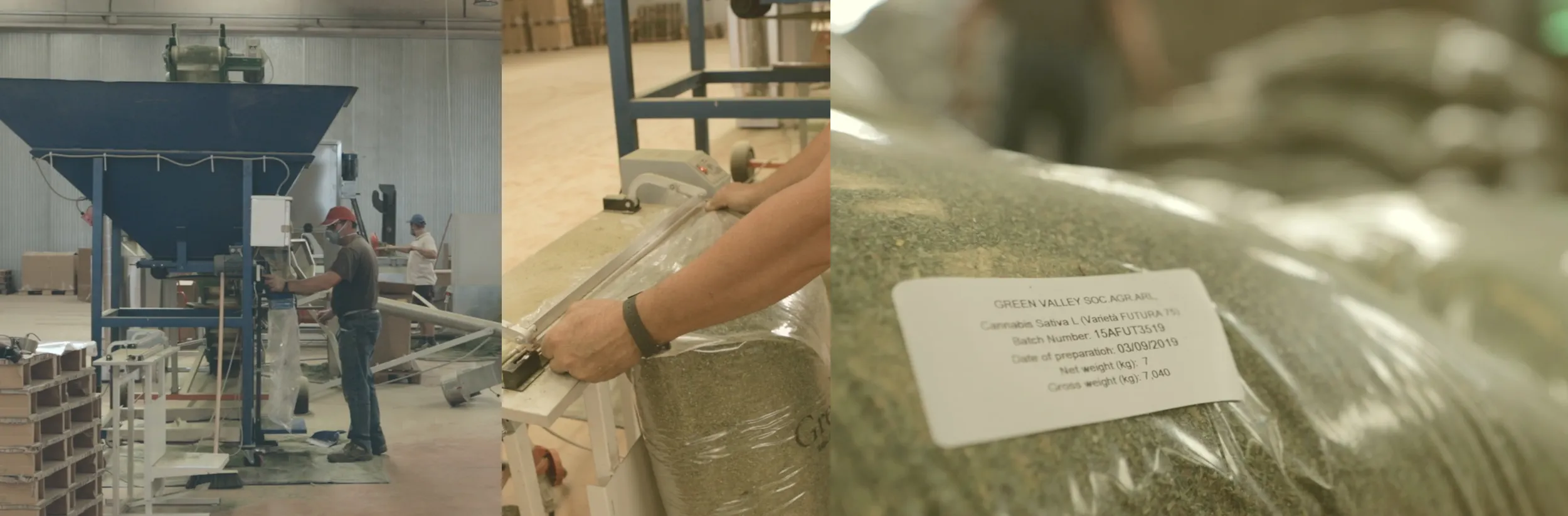
Once the separation process is complete, the ground material moves directly from the separating machine to the specific exit mouths, which have bags at their ends (specifically intended for food use, clean and dry, allowing for transpiration but not contact with external substances/possible contaminants) for the final packaging. The machine cycle therefore allows for controlled and continuous filling (reducing the passing and intervention of operators). However, we highlight the fact that all the material used during the different processing phases is registered and comes with technical data sheets attesting to its compatibility and utility for our qualitative aims and objectives.
The packaged material, therefore, is stored on pallets. In this phase the final labelling of homogenous lots occurs, with an individual lot number summarising all processing data, allowing clear and precise product traceability. The pallets are stored in specific well-ventilated areas of the warehouse, with protected accesses, and spaces are easy to clean and subdivided by processing phase. Once the packaging process is complete, the material waits to be shipped to our production site (or to clients).
CBD OIL PRODUCTION
To obtain an extract, the interesting compounds of the plant need to be separated from the ones which have no use for us. More specifically, every Enecta extract is developed and formulated around a specific cannabinoid. Cannabinoids can be separated from the plant matter in many different ways. We have developed specific methods to ensure both safety and efficiency of this process. This is why we can guarantee that the best CBD oil can also be affordable for our clients.
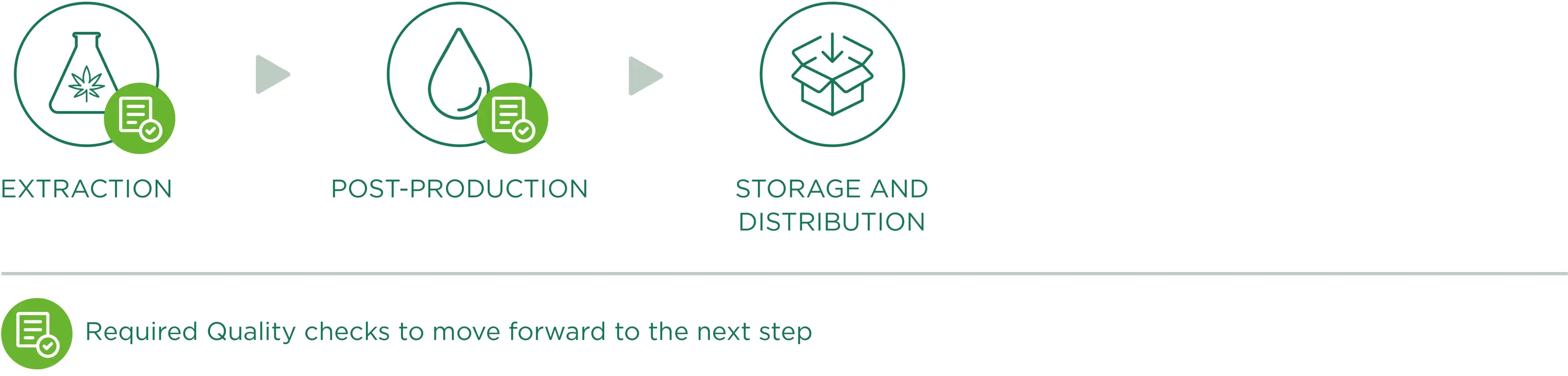
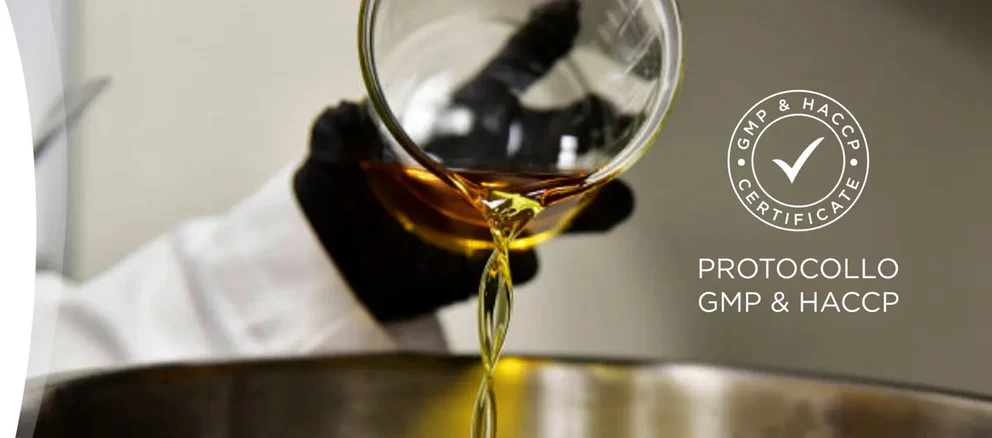
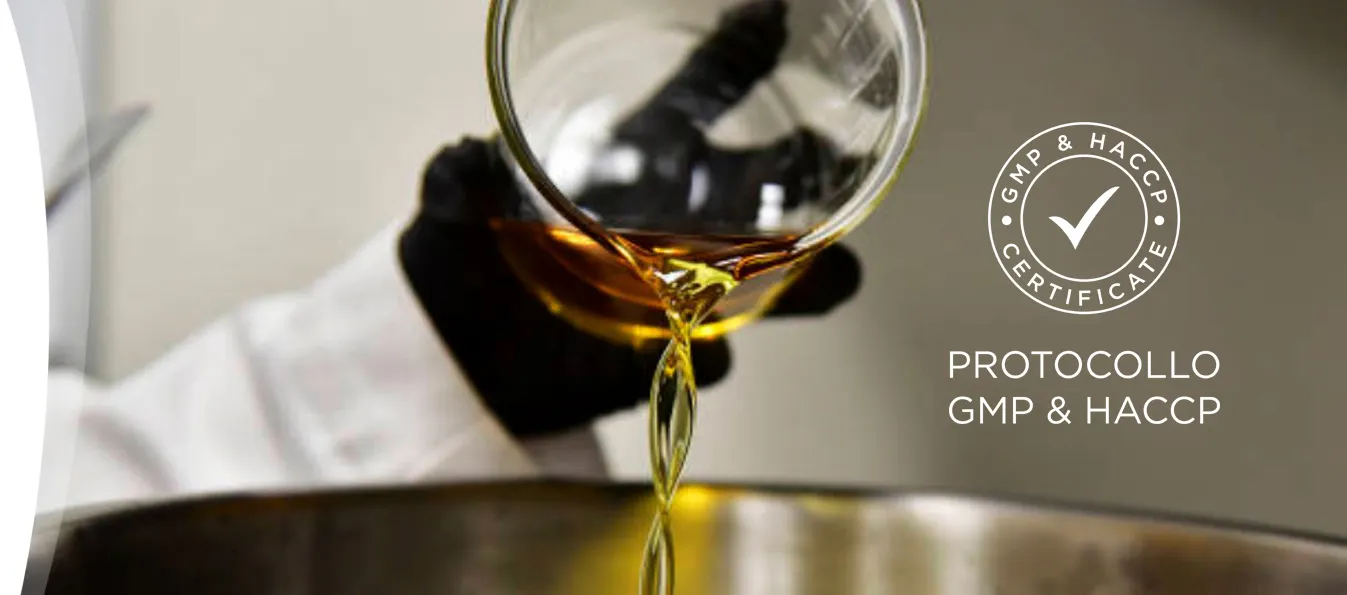
Pharmaceutical guidelines
The packaged and stored hemp is ready to be shipped to our production site (or to clients), where the plant material will undergo further processing to obtain the final product. Our priority is to maintain high quality management standards in the development, production and control of our products, in order to guarantee that they meet safety, quality and efficiency requirements simultaneously.
All production phases follow the GMP requirements (Good Manufacturing Practice, rules and instructions applying to all stages of the production cycle) and are based on a reliable integrated quality system and accurate risk management procedures, to guarantee that the products are in compliance
with the ICH (The International Council for Harmonisation of Technical Requirements for Pharmaceuticals for Human Use) stability guidelines, the ISO (International Standard Organisation) quality regulations and that they are therefore suitable for the intended use and does not present a risk to the consumer because of inadequate safety or quality precautions.
This quality objective is achieved both through the work of the well-qualified personnel involved in all processing phases, and by using certified procedures on the premises and spaces, with suitable equipment and services.
CBD oil extraction
A key role of production is the chemical extraction phase which happens in laboratories where all operations are planned, checked, recorded and reported. Chemical extraction consists in separating the interesting components (i.e. CBD, CBG) from the solid plant matrix, so as to only obtain rich/concentrated extracts of these components of interest, with an accurate removal of THC. The applied extraction methods enhance the properties of our raw material, maintaining the structure and original biological activity of its substances.
The extraction conditions are accurately standardised, with special attention to process parameters including temperature, extraction agent and reagents used. Our process involves the use of GRAS (Class III) solvents like EtOH; the different following steps ensure the separation of interferents (like wax) that would disturb the purification and isolation phases of a specific Cannabinoid, which should happen without degrading its natural molecular structure. Such a structured process allows us to work on the acid components (i.e. CBDA) to be decarboxylated if necessary, reducing the formation of secondary process metabolites.
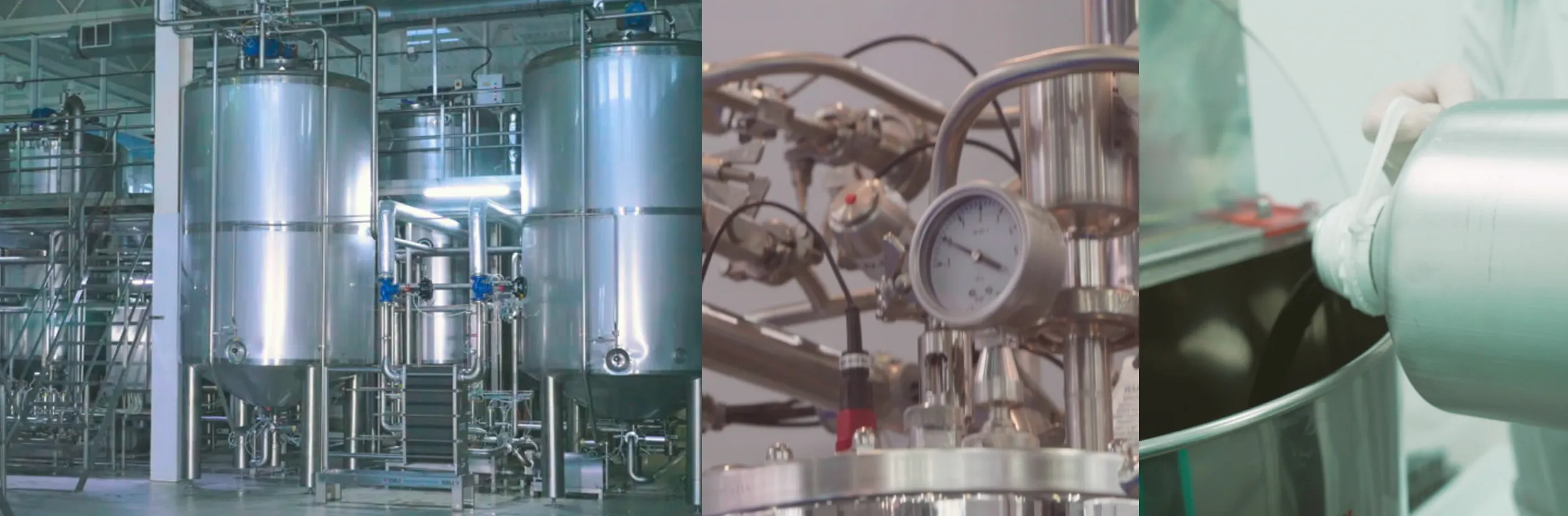
Quality control
Quality control approves and implements allquality control procedures: putting in writing the detailed procedures forsampling and in- and post-process testing; keepingproduction documentation and records; defining the cleaning and sanitising procedures of the premises; checking operating conditions (calibration and maintenance) of tools, machinery and equipment; monitoring process efficiency; guaranteeing correct container labelling andpackaging conformity; monitoringproduct stability; implementing effective traceability systems. Quality control is therefore not limited to laboratory operations as it is involved in all decisions regarding the quality of the product (from growing the raw material to packaging and distributing the final product).
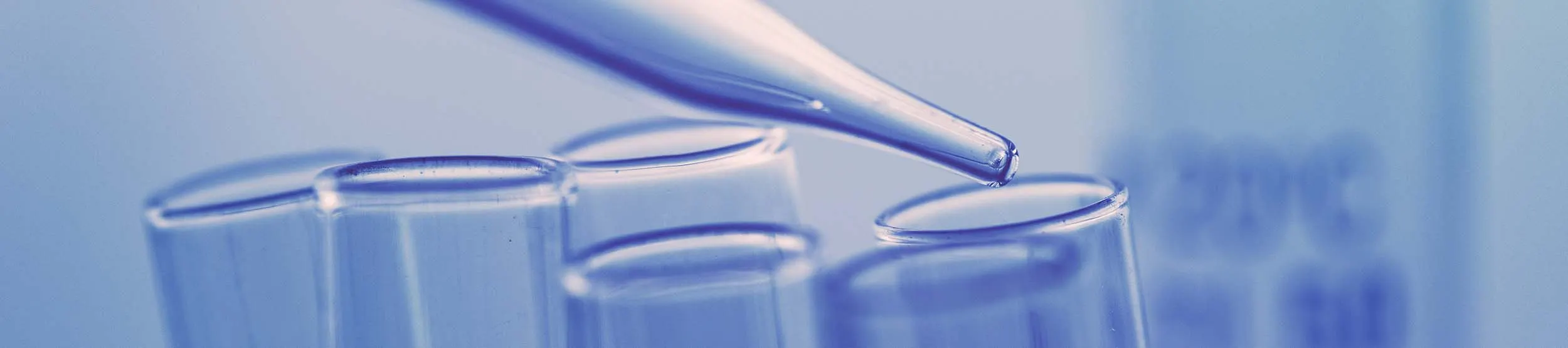
Post-production
As for product packaging, it can be divided into different categories, based on the purpose and the role in the production chain. By “packaging” we mean the enclosing material intended to contain the products and ensure their protection, presentation and allow them to be handled safely from producer to consumer.
In general, packaging can be divided into primary and secondary. The first category refers to containers directly in contact with the product (i.e. vials, bottles), while the second categoryconsists in the packaging enclosing the primary material (i.e. cases for small bottles etc).
The purpose of quality packaging, that is, what is asked to ensure the consumer is:
- Perfectly adapted to the product,ing protect its integrity and preventing any potential penetration from external agents;
- Effective resistance to external environmental conditions (particularly for primary packaging, which should be light-resistant and airtight);
- Adequate product protection with precise characteristics to guarantee the integrity of the product during movement or transportation;
- Correct communication on the nature of the contents.
The products, in fact, can deteriorate due to chemical incompatibility between formulation components or with packaging materials, or even the effects of humidity, oxygen, light and various temperatures. For example, using opaque containers (made of metals, coloured plastic or amber glass) allows you to protect the product from light and oxidation reactions. The packaging will contain the product lot number for traceability and to have the necessary information to identify the product (name, qualitative and quantitative composition, expiry date), allowing its authenticity to be traced. The traceability is a process that follows the product from upstream to downstream in the production chain and ensures that, at every stage, appropriate traces (information) are present and included in the creation of the lot number.


Storage and distribution
The places dedicated toproduct storageare designed to: ensure good storage conditions; allow the orderly and categorised storage of goods andreduce the risk of contaminationto a minimum; overall, to prevent any negative effect on thequalityof the products; to maintainadequate storage conditions(light, temperature, humidity etc.) and therefore, to keep the quality and integrity standards constant during both storage and transportation.